Uneven Cake
Under-loaded goods in the press may cause uneven force distribution between the goods and the diaphragm. This creates an uneven cake, which can lead to undesired stress on the diaphragm with shearing on the high load side and stretching on the low load side. This occurrence is displayed on the image below.
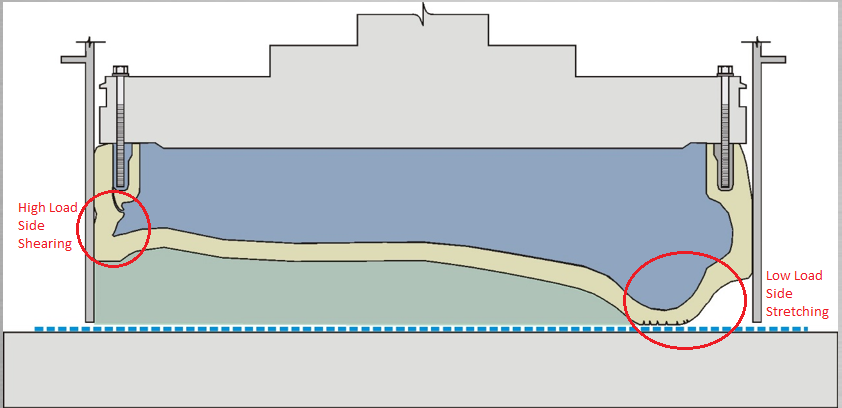
On the high load side, the pressure on the heel overcomes the pressure on the side wall, at which the heel is pushed upwards and collapses. On the low load side, the diaphragm is expanded to fill the void on the press bed, where it stretches and exceeds its elastic yield strength; this leads to cracks on the rubber and weakens the diaphragm until it blows out.
Diaphragm Filling
An improperly-filled diaphragm can either be under-filled or over-filled. Possible causes include improper installation, excessive wear, and lack of maintenance.
With an under-filled diaphragm, excessive force is exerted on the heel of the diaphragm, pushing it upward as shown in the image below. This is similar to what happens to the high load side of an uneven cake, except that the force occurs around the entire circumference of the diaphragm edge in this case.
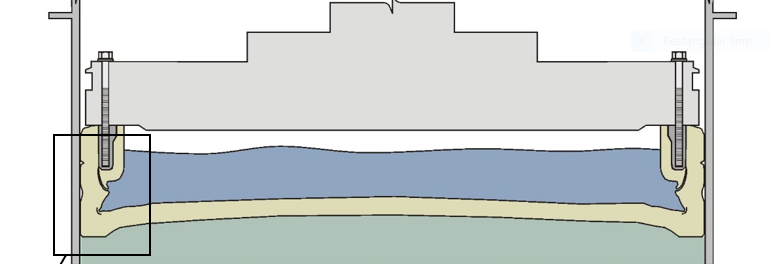
Improper filling and shaping can lead to an over-filled diaphragm as shown below. With too much fill, the center of the diaphragm comes into contact with the goods before the outer area, leaving an air gap around the circumference. Stretching can occur at any point around the outer area of the diaphragm, which may lead to cracks on the rubber surface.
Maximizing Diaphragm Life
Over time, the cyclic compression that a gum rubber diaphragm withstand during operation may cause it to deform and shrink in size, which would lead to under-fill. A remedy for this would be to add more gum rubber sheet(s) to the diaphragm once deformation occurs. Milnor offers 1/8" gum rubber sheets with the following part numbers:
MP15xx (36" Diameter Diaphragm)
Full Set ACW10012A
MP16xx (40" Diameter Diaphragm)
Full Set ACW10010A
MP1Axx (48" Diameter Diaphragm)
Full Set ACW10011A
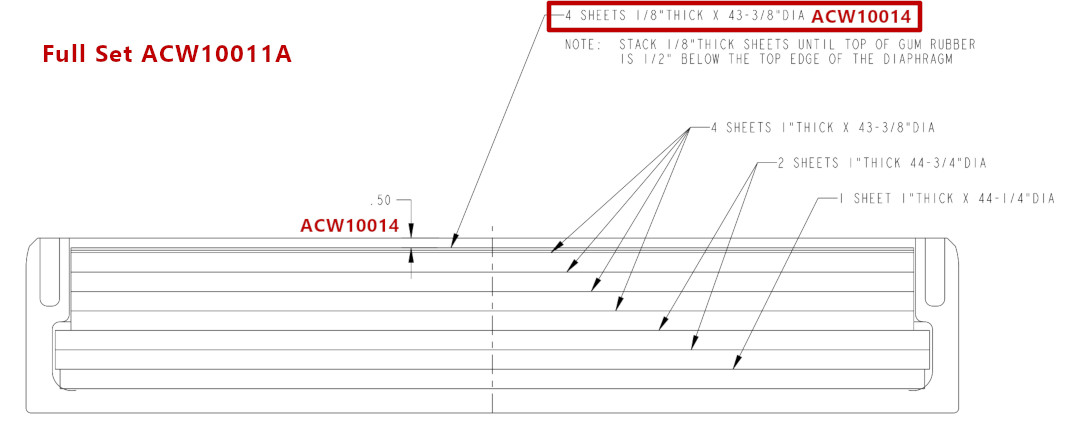
For presses with water-filled diaphragm, it is highly suggested to switch to gum rubber. Using gum rubber eliminates the need to seal the membrane to the platen and check fill water levels. Use the appropriate gum rubber sheets as listed above to add gum rubber to the diaphragm. Make sure the gum rubber stack height is within 1/8" from the top of the diaphragm ring.
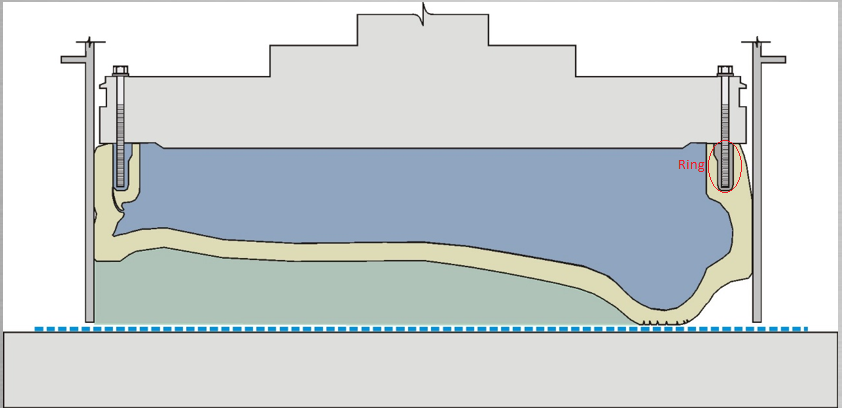
To prevent uneven cake distribution, avoid under-loading goods into the press as much as possible. Another method to consider is to control water levels in the last module of the CBW by changing weir levels. Extra water can help distribute goods evenly over the can. However, too much water can create excessive momentum as goods slide down the chute and towards the far edge of the can.