A quick exhausts vents pressure from a large volume device, i.e. an air cylinder and push downs (Firestone air mounts). This allows the Cylinder or air bag device to get in a ready state (completely exhaust) more rapidly than relieving the pressure back through the valve that supplies air to the device.
The incoming air that is fed through the quick exhaust seals the exhaust port and sends the air towards the air cylinder or component.
When the incoming pressure turns off, the seal to the exhaust port is broken (or popped open) and dumps a large volume of air out of the exhaust port.
Why does a quick exhaust fail?
The quick exhaust diaphragm has a tough life. It seals the air pressure in the device and this causes small indentations in the diaphragm. After a while the diaphragm gets "punched out" and will leak when it should seal (when we want the device to be charged with air) .
On 2 stage presses there is an additional failure possibility. In the event of an emergency stop while the pre press air cylinder is in motion, the diaphragm takes a serious inrush of pressure. This may cause it to tear or perforate immediately. This has to do with the safety solenoid circuit operation and results thereof. This would occur when someone opens the doors on the pre press and breaks the safety circuit. The inertia of the cylinder actually helps create excess pressure.
If you hear a quick exhaust leaking, replace the diaphragm. On a 2 stage press the air exhausts into the air accumulator (oil separator) and you will hear the air leaking. You must listen to each quick exhaust individually with a stethoscope to know which one is leaking.
Quick exhausts can be replaced or repaired.
Below, you can see the air flow during pressurizing, exhausting, and when a quick exhaust is in failure mode.
Pressurizing the Cylinder
Exhausting the Cylinder
Quick Exhaust in a Failure State
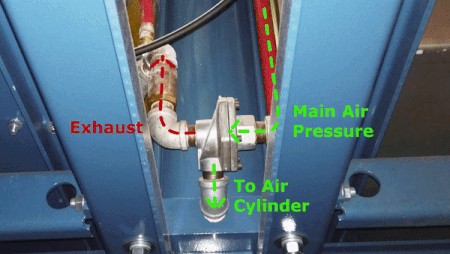