The issues here relate to optimizing the performance of a Milnor gas dryer with an Eclipse Air Heat (AH) burner.
also known as: 64058 testing and tuning instructions
Topics are:
- Combustion air diffuser plate and fan cleaning
- Burner firing
- Inlet temperature sensing
- Burner minimum fire setting
- Needle valve adjustment for pilot flame
- Plastering of goods
- Burner flame-out while at higher fire positions.
- Main air damper position
Check and correct as needed the following items to produce repeatable results from the dryer. If dryers are in a group (as in an automated system) the dryers will perform similarly if these adjustments are made and maintenance performed regularly. To avoid making unnecessary adjustments, remember that the dryer operated without pressure switch trips and flame out conditions when it was new. The settings of the pressure switches and pilot gas will not change unless someone changes them. So, do not adjust the switch, but instead find and fix the variable that changed. This could include lint buildup on the combustion air diffuser screen and the combustion blower.
Dryer Burner Combustion Air
- To burn gas efficiently and safely, the dryer burner MUST have combustion air. The Eclipse AH burner needs about 1200 CFM to properly burn. This requires a clean combustion air filter and a clean combustion air diffuser screen. The big idea… if you see yellow flame then you have a combustion air deficiency. The burner and the burner enclosure will also reach damaging temperatures if the flames get too long as a result of low combustion air.
- The Milnor manual recommends that the combustion air diffuser screen be cleaned regularly. To make this easy to accomplish, you can use compressed air and an air wand inserted into the back of the combustion air chamber in the burner. See the picture below for the hole location for modification of the burner. An air wand can be fabricated locally or bought from Milnor (PN: W7 71558 ) for this use. The air wand is made of 3/8" stainless tubing with a 3/8” FPT fitting welded on the end. The other end is welded closed and 3 3/32” holes are drilled in the side of the tube at the closed end. The air wand is inserted into the burner behind the combustion air diffuser screen and blows lint accumulation through the screen into the burner box. This cleaning procedure is the single best assurance of a properly firing burner.
- The hole location for the combustion burner box is shown below in Fig. 1. It is directly between the bottom and top of the burner combustion air box and 1” from the back of the enclosure. This hole can be left uncovered during normal operation. The hole can be drilled on either side of the burner allowing for easiest access. The cavity inside allows combustion air to flow through the air diffuser screen evenly, allowing for an even burning of gas over the burner face.
- The combustion air fan blades should be cleaned each time you blow down the combustion air diffuser screen. In order to gain easy access to the fan, a hole can be drilled into the shroud. Insert the tip of a low pressure air gun into the hole and blow down the fan. You should be able to direct the nozzle and the resulting air stream from side to side to clean the fan. The hole location for the combustion air fan is shown below in Fig. 2. It is located on the fan shroud at either the 4:30 or the 10:30 position depending on the shroud mounting the combustion burner box. Inside this shroud is a squirrel cage fan. When drilling, be careful to not drive the drill bit into the fan vanes. This would damage the fan.
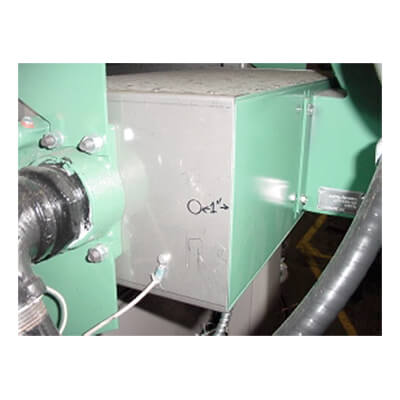 |
Figure 1
Burner Box blow down hole location - to be drilled on site using 1/2" to 9/32' drill bit. Burner can be drilled on either side (not both) allowing for easiest access. |
Figure 2
Combustion Air Blower Shroud blow down hole location – to be drilled on site using a 3/8” to 7/16” drill bit. Some blower shrouds are mounted up as shown with the motor/fan above the burner box and some have an alternative mount with the motor/fan mounted below the burner box. The hole will be at about the 4:30 position as shown or at the 10:30 position if the alternative mount. (Drill carefully to not drive the drill bit into the vanes of the squirrel cage blower wheel.) | 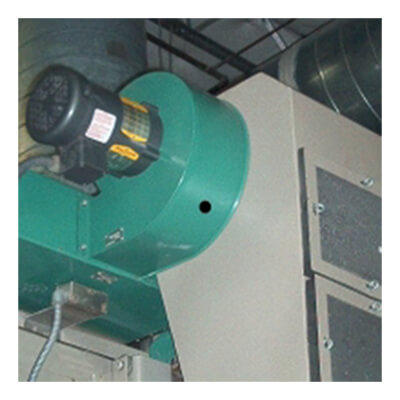 |
- The combustion air inlet may have a fixed position air dampener (a round disc) on the inlet side of the fan blower. This is there to limit the air for proper fuel to air mixture in the burner. The setting of the disc is critical to proper burn and emissions. If anyone adjusts this in the field by mistake, the plate will have to be readjusted back to the Milnor specification of .9" of combustion air pressure at the switch. The combustion air switch needs to be set at .6". Burners without the disc may have a slightly higher differential pressure at 1.1".
- Improper combustion air can seriously affect performance and proper lighting of the burner. Always clean these areas before attempting any checks or adjustments to the burner or air switches.
Inlet Temp Sensing:
On dryers produced before July of 2005, check the insertion depth of the inlet temp probe. The inlet temperature probe needs to be pulled out of the shell cavity to the limit of the enclosure guarding the probe. This would have the probe inserted approximately 8 1/2 inches with the wired end of the probe touching the external cover. This helps sense the highest temperature air stream.
Note: If the dryer is flaming out and producing a sawtooth graph, like the one below, for the inlet temperature, the inlet probe is probably not set at the proper depth.
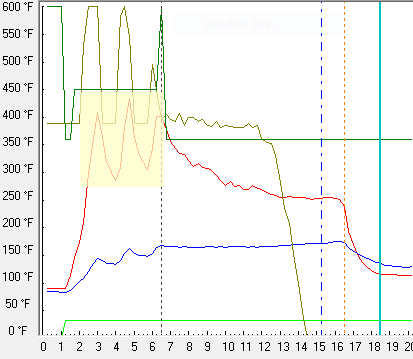
Plastering of goods:The direction of the basket rotation must be as follows: on a left dryer, the basket must turn counterclockwise when in the loading operation. On a right hand dryer, the basket must turn clockwise when in the loading operation.
Thus, in manual output operation, the right dryer runs CCW when CW is commanded. This is done by wiring the CW wire into the CCW input (and CCW into the CW) at the inverter. If this is not the case then flip the wires on the S1 and S2 terminals of the inverter.
- The dryer has the tendency to plaster goods with air flow in one direction. We reduce the speed of the basket in the direction that encourages plastering. This lets the goods fall at the same angle in the basket to prevent plastering. There is actually a 9% change in speed as the basket is reversing in one direction from the other. Make sure that the “hardstart” constant in dryer configuration is set to a 1 to enable this feature.
- To ensure that all dryers run the same basket speeds at 100% rotation speed, the frequency bias gain should be set the same in each dryer’s inverter. On V7 (or GPD315) inverters, constant No. N61 (frequency bias gain) should be set to zero. Changing the gain will affect the speed at which the basket turns. Since the output voltage of the D/A board cannot be modified, the inverter (constant N61) is modified, if needed, to make all dryers in a group turn at the same speed when 100% speed is commanded from the dryer programming. Most dryer inverters will be programmed with N61 at 0 (zero). There may be a case in order for one specific dryer to turn at the same speed as the other dryers in the group, that the speed may have to be increased/decreased using N61.
Minimum Fire Setting on the Gas Valve:
The minimum fire settings on the dryer must be set absolutely consistent from one dryer to the other. Set this by measuring the output temperature at minimum fire and adjusting the minimum fire setting on the gas valve to achieve a 75 degree gain over ambient air temperature. (Example: if the ambient air at the inlet is 75 degrees then the outlet temp target is 150 degrees). This is a good technique to use for both propane and natural gas. The approximate minimum fire modulating valve position for natural gas is 20 degrees open. Propane dryers have been set at Approximately 17 degrees open in the factory but must be checked on installation with the fuel source used at the site. In natural or propane systems the 75 degree gain over ambient temperature is the proper target. Set up a dry code to run at minimum fire setting. Then read the indicated temperature on the screen. It should be 75 degrees above ambient air temperature. Adjust the gas valve as per the Dryer Service manual. Remember that a minimum fire position set too low can allow raw gas to not burn at the burner. The flame should be inspected at minimum fire to ensure a complete burn across the burner.
Pilot Gas Needle Valve adjustment:
Intermittent firing may occur when the pilot gas does not properly engulf the flame rod. This can be caused by a clogged combustion air diffuser screen, so check this first. In some cases the problem is caused by excess pilot gas and a pilot flame that does not engulf the flame rod. You can check the voltage on the flame rod at the fire eye unit and adjust the needle valve to achieve the highest voltage throughout the firing sequence. In some cases the flame is actually pushed away from the flame rod by raw gas from the main burner ports. This again is probably tied to the lack of combustion air.
If flame out occur after these checks are made, call Milnor Tech Support to discuss adding a burner port plug. These burners need a total of 3 plugs. See the picture. The main ports will push raw fuel into the flame rodord and prevent sensing of a flame. Reducing the pilot will help keep the flame on the flame rod. a 1/8" rivet can be used as an additional port plug.
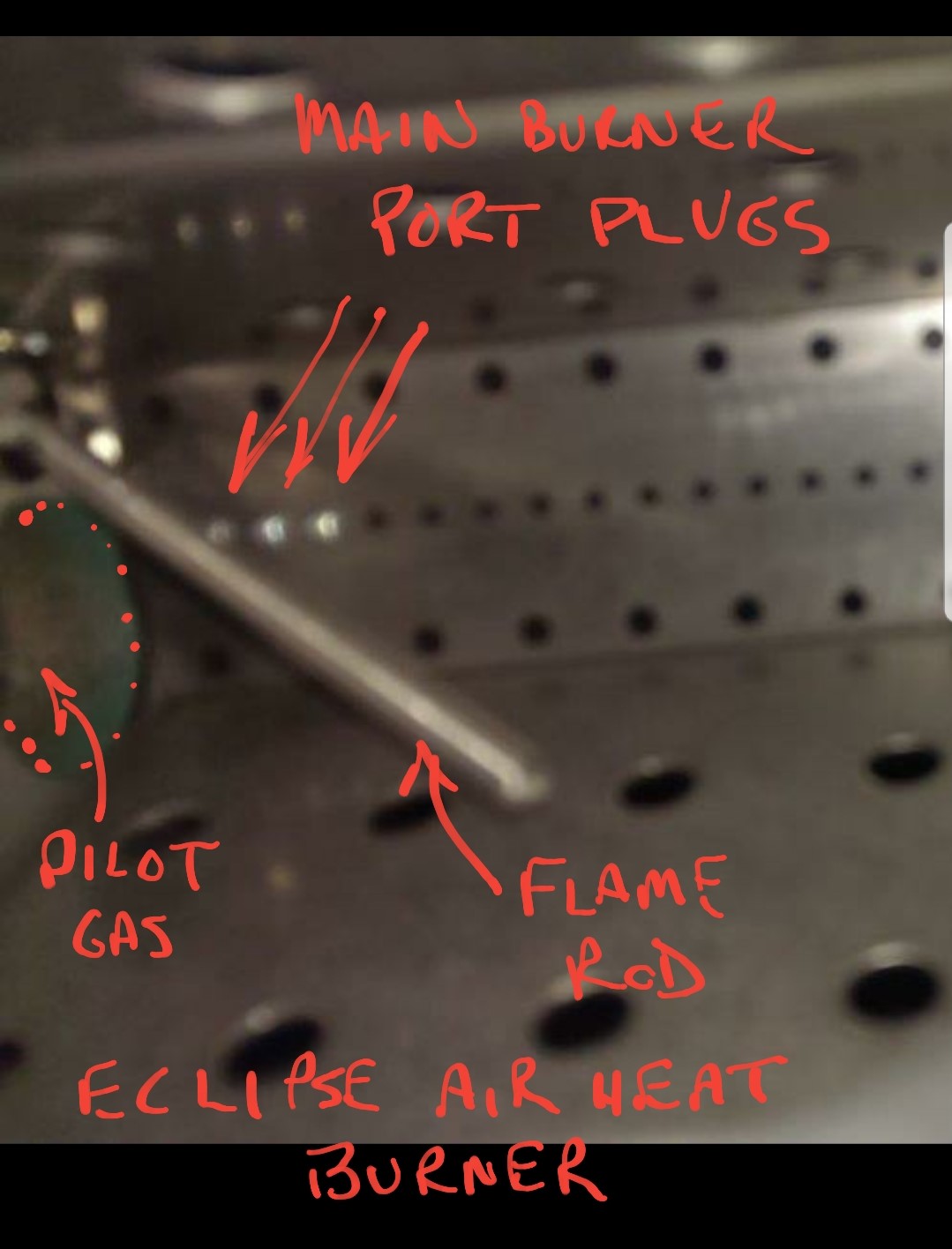
Main Air Damper Position:
We know that the main air damper and the associated air cylinders are set in a consistent manner at the factory. However we have heard that these air cylinders are adjusted by some technicians in the field to help achieve a lower air flow for sensitive goods. This introduces another variable to the air flow. Make sure that all dampers in a dryer group are adjusted the same.
As with all Milnor dryers in a given group, each dryer must be set with the same physical characteristics as its sister dryers so that the dry codes (or formulas) will operate consistently in all dryers. The technician should make every effort to ensure these above parameters are consistently adjusted to achieve the best results from the dryer group.